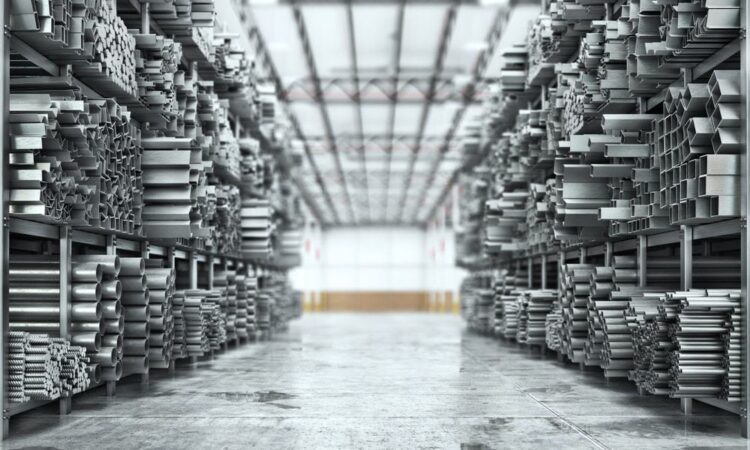
M50 and C465 Alloys in Aerospace Engineering
M50 Alloy Overview
M50 alloy, primarily known for its high strength and resistance to wear, is a high-speed tool steel frequently utilized in aerospace engineering, especially in bearing applications. M50 exhibits exceptional fatigue resistance and toughness, making it an ideal choice for critical aircraft components like jet engine bearings, where reliability and durability are paramount.
C465 Alloy Overview
C465 alloy’s adaptability in various environmental conditions, coupled with its resistance to stress corrosion cracking, underscores its relevance in modern aerospace engineering.
Material Properties and Characteristics: M50 vs. C465
Strength and Hardness
M50 alloy’s strength and hardness are its standout features, especially at elevated temperatures. C465, in contrast, offers a unique blend of high strength and ductility, thanks to its age-hardening process.
Corrosion Resistance
Corrosion resistance is a critical factor in aerospace applications, and here, C465 stands out. Its composition, including elements like nickel and chromium, provides excellent resistance to a variety of corrosive environments, including those experienced in aerospace settings. This makes C465 an ideal choice for parts that are exposed to harsh conditions, including saltwater and high humidity environments.
M50, while primarily focused on strength and wear resistance, offers moderate corrosion resistance, which is often enhanced through coatings or surface treatments. This makes M50 suitable for internal components like bearings, where corrosion resistance is important but not the primary concern.
Application Suitability
M50’s application in aerospace is predominantly in areas subjected to high stress and temperatures, such as engine bearings and other high-speed rotating components. Its ability to maintain integrity under such conditions makes it an invaluable material in these applications.
C465, with its unique combination of strength, ductility, and corrosion resistance, finds its application in structural components of aircraft. Its ability to withstand various types of stress and environmental conditions makes it suitable for critical components like airframe structures and fittings.
Aerospace Industry Applications: M50 and C465
M50 Alloy Applications in Aerospace
The M50 alloy is particularly esteemed in the aerospace industry for components that are subjected to extreme stress and high temperatures. Its primary applications include:
- Jet Engine Bearings: Due to its high-temperature strength and excellent wear resistance, M50 is widely used in manufacturing jet engine bearings. These bearings must endure extreme stress and temperature fluctuations, making the durability and toughness of M50 crucial.
- Turbine Blades and Disks: The alloy’s resistance to thermal fatigue and high-temperature strength make it suitable for turbine blades and disks, which are core components of jet engines.
- High-Speed Gear Components: The high strength and hardness of M50 are beneficial for gear components in aerospace applications, particularly where high-speed operation and reliability are essential.
C465 Alloy Applications in Aerospace
C465, known for its unique combination of strength, ductility, and corrosion resistance, finds its applications in different aerospace contexts:
- Aerospace Structural Components: Its excellent strength-to-weight ratio makes C465 ideal for structural components of aircraft, such as frames and supports that require both durability and lightness.
- Fittings and Fasteners: The alloy’s resistance to stress corrosion cracking and its high strength are critical for fittings and fasteners in aerospace, ensuring secure and durable connections in aircraft structures.
- Landing Gear Components: The toughness and corrosion resistance of C465 make it suitable for landing gear components, which must withstand significant stress and potentially corrosive environments.
Cost Analysis and Affordability
Cost Factors for M50 Alloy
- Raw Material Costs: The cost of raw materials like molybdenum and vanadium in M50 contributes significantly to its overall cost. These materials are essential for the alloy’s high-performance characteristics but are often expensive.
- Manufacturing Complexity: The production process of M50, including forging and heat treatment, is complex and energy-intensive, adding to the cost.
- Specialized Processing: M50 often requires specialized processing like vacuum melting to achieve its desired properties, which can increase production costs.
Cost Factors for C465 Alloy
- Composition Costs: The cost of nickel, chromium, and molybdenum, which are key constituents of C465, influences its overall price. The fluctuating market prices of these metals can impact the alloy’s cost.
- Age-Hardening Process: The age-hardening treatment that C465 undergoes is an additional step in its production, contributing to higher manufacturing costs compared to simpler stainless steels.
- Demand and Availability: The specialized nature of C465 for certain aerospace applications can affect its market availability and price, especially under fluctuating demand in the aerospace sector.
Affordability Comparison
In general, both M50 and C465 are considered premium materials in the aerospace industry, with their costs reflecting their high-performance characteristics. M50, with its focus on high temperature and wear resistance, often incurs higher costs due to its specialized manufacturing processes and raw material costs. C465, while also expensive due to its unique composition and age-hardening process, may offer a cost-benefit in applications where its combination of properties is essential.
Supplier Landscape and Availability
M50 Alloy Supply Chain
- Specialized Steel Manufacturers: M50 alloy is typically produced by specialized steel manufacturers who cater to the aerospace and defense industries.
- Regional Availability: M50 is more readily available in regions with a strong aerospace manufacturing presence, such as the United States, Europe, and parts of Asia. In these regions, the supply chain is well-established, with multiple suppliers offering various grades of the alloy.
- Custom Orders and Lead Times: For specific aerospace applications, M50 may need to be custom-ordered, especially for unique compositions or treatments. This can affect lead times and availability, requiring advanced planning for procurement.
C465 Alloy Supply Chain
- Premium Stainless Steel Producers: The production of C465 is usually undertaken by premium stainless steel producers who have the expertise in age-hardened stainless steels. These suppliers are fewer in number compared to standard stainless steel producers.
- Global and Niche Suppliers: While C465 is available globally, its production is often limited to a few key suppliers who specialize in aerospace-grade materials. This can lead to a more niche market, with focused supply chains.
- Supply Consistency and Customization: The supply of C465 can be consistent, but like M50, it may require custom orders for specific aerospace applications. The age-hardening process and composition adjustments can impact delivery times.
Performance Comparison in Aerospace Environments
M50 Alloy Performance
- High-Temperature Strength: M50 excels in maintaining its strength and hardness at high temperatures, making it ideal for engine and turbine components that operate under extreme heat.
- Wear Resistance: Its exceptional wear resistance ensures longevity and reliability in components like bearings and gears, which are subject to continuous friction and stress.
- Fatigue Resistance: M50’s fatigue resistance is a key attribute in aerospace applications where components are subjected to cyclic stress, helping to prevent premature failure.
C465 Alloy Performance
- Strength and Ductility: C465 stands out with its rare combination of high strength and ductility, allowing components to withstand high loads while maintaining some level of flexibility, crucial in dynamic aerospace environments.
- Corrosion Resistance: In corrosive environments, C465 provides superior performance, resisting various forms of corrosion, which is vital for airframe components exposed to harsh conditions.
- Stress Corrosion Cracking Resistance: This alloy is particularly resistant to stress corrosion cracking, a critical feature for structural components in aircraft that are exposed to tensile stress in corrosive environments.
Comparative Analysis
In high-stress aerospace environments, both M50 and C465 demonstrate exceptional performance, albeit in different aspects. M50 is more suited for applications where high temperature and wear are major concerns, such as in engine components. C465, with its balanced strength, ductility, and corrosion resistance, is more adapted to structural applications where a combination of these properties is crucial.
Aerospace Manufacturing Processes
M50 Alloy Impact on Manufacturing Processes
- Machining and Tooling Requirements: The high strength and hardness of M50, particularly after heat treatment, pose challenges in machining. It requires specialized tooling and techniques, often involving carbide or other hard materials, to effectively machine without excessive wear on tools.
- Heat Treatment Complexity: M50 requires precise heat treatment to achieve its desired properties, including hardenability and wear resistance. This necessitates sophisticated heat treatment facilities and processes, which can add complexity and time to the manufacturing process.
- Quality Control and Testing: Given its use in critical high-stress components, M50 necessitates stringent quality control measures. This includes detailed testing for properties like fatigue strength, hardness, and structural integrity, ensuring that every component meets the rigorous standards of the aerospace industry.
- Cost Implications: The specialized machining, heat treatment, and quality control processes required for M50 increase manufacturing costs. This must be factored into the overall cost-benefit analysis when choosing M50 for specific aerospace applications.
C465 Alloy Impact on Manufacturing Processes
- Age-Hardening Process: The age-hardening process of C465 adds an additional step in the manufacturing process. This treatment is essential to develop its unique combination of strength and ductility, but it also requires precise temperature control and timing, adding to the manufacturing complexity.
- Machinability and Formability: C465, while strong, is generally more machinable than M50, especially in its solution-treated condition before age hardening. This characteristic allows for more ease in shaping and forming the alloy into various aerospace components.
- Corrosion-Resistant Fabrication: The excellent corrosion resistance of C465 reduces the need for additional protective coatings or treatments, simplifying certain aspects of the manufacturing process. However, this also means that any machining or welding must be carefully managed to maintain the alloy’s corrosion-resistant properties.
- Specialized Welding Techniques: When welding is required, C465 demands specialized techniques to retain its properties post-welding. This includes considerations for heat input, filler materials, and post-weld heat treatment.
Comparative Impact
Both M50 and C465 alloys impose unique requirements and challenges on aerospace manufacturing processes. M50’s hardness and need for precise heat treatment make its machining and production more complex and costly, suited for high-performance applications where its properties are indispensable. C465, with its age-hardening process and better machinability, is easier to work with but still requires specialized handling, particularly in welding and heat treatment.